Puertas de inyección
Procesos > ► Inyección > ► Sobremolde
Canales
El sistema de alimentación de moldes, es decir, todo el sistema de canales que lleva el polímero fundido a las cavidades a llenar, afecta significativamente la calidad de los productos moldeados, así como los costos del molde y el moldeo. Un sistema de alimentación tradicional generalmente consiste en una boquilla caliente y elementos fríos que se extraen junto con la pieza. Los elementos fríos del sistema de alimentación toman el nombre de riser y suelen ser: la zanahoria (sprue), los canales (runners) y la inyección (gate). La boquilla de la prensa es esencialmente un canal caliente que conecta la cabeza de la cámara de plastificación al núcleo del molde. De hecho, se pueden distinguir dos tipos de canales de alimentación: caliente y frío. Los primeros están contenidos en un bloque calentado especial llamado múltiple o distribuidor, que opera a temperaturas muy altas, es decir, temperaturas equivalentes a las de la masa fundida. El molde prototipo, que es el tema de este trabajo, consiste solo en canales fríos, trabajados directamente en los troqueles del molde. Se solidifican junto con el producto después de cada inyección y se extraen en cada ciclo para ser posiblemente reciclados.
La puerta, por otro lado, es la conexión entre el edificio y los canales; Por lo general, es un área limitada que facilita la separación del canal de la pieza. La puerta debe garantizar el correcto llenado y mantenimiento de la pieza, así como facilitar la separación de la pieza de trabajo potencialmente automática de los canales. La forma, posición y tamaño de la puerta son parámetros fundamentales a tener en cuenta para su correcto diseño. La sección transversal de la compuerta debe ser relativamente pequeña para permitir una fácil extracción del bebedero y al mismo tiempo no demasiado pequeña para no limitar la fase de compactación evitando que la puerta se congele por adelantado, generalmente se recomienda un grosor o un diámetro de la puerta entre el 40% y el 70% del espesor de la pared de la parte a la que está unida. La longitud de la compuerta debe ser lo más pequeña posible para reducir la caída de presión y mejorar la compactación. Se recomienda tener longitudes entre 0,75 y 1 mm.
Existen diferentes tipos de inyección y diseño de compuerta de acuerdo con diferentes necesidades:
- inyección directa
- inyección capilar
- inyección de disco
- inyección a plátano
- inyección a película
- inyección submarina
La inyección directa es diferente de los otros tipos de inyección, ya que la zanahoria alimenta directamente la pieza a imprimir e implica la necesidad de una costosa operación de extracción en el caso de una zanahoria fría.
Inyección submarina
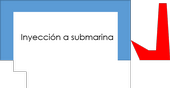